The connection between the MRC01 and host system is controlled directly via EtherNet/IP™. Custom-built robots can be added easily, without the need to make major changes to the control system from the existing equipment.
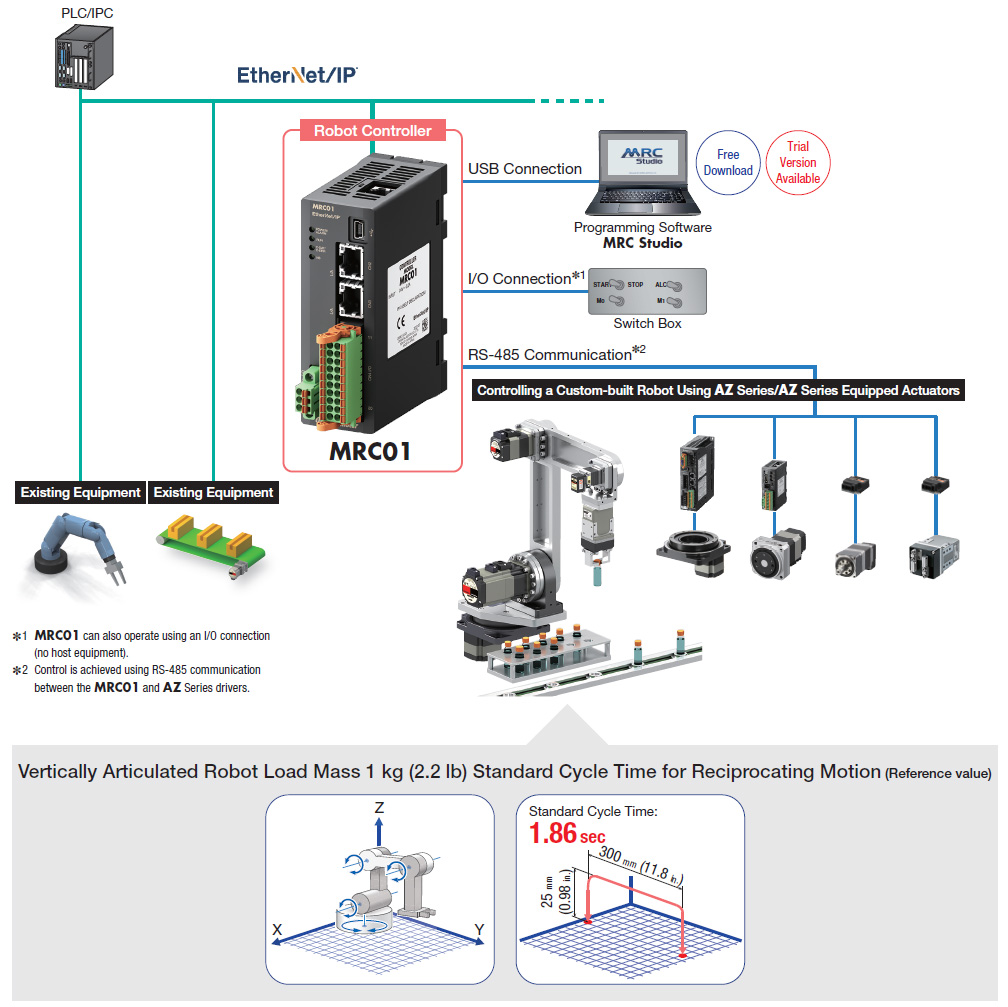
The "Programming Software MRC Studio" has been prepared to simplify setting up custom-built robots from the initial setting step to the operation programming step. A trial version of the programming software is also available to allow customers the chance to experience the operation of the MRC01 before purchase.
STEP 1 - Easy Setup with Step by Step Guidance
Initial settings are made using a wizard to select the robot type and input mechanism information.
By following the guidance instructions while looking at the illustrations, even absolute beginners can quickly set up a robot's initial settings.
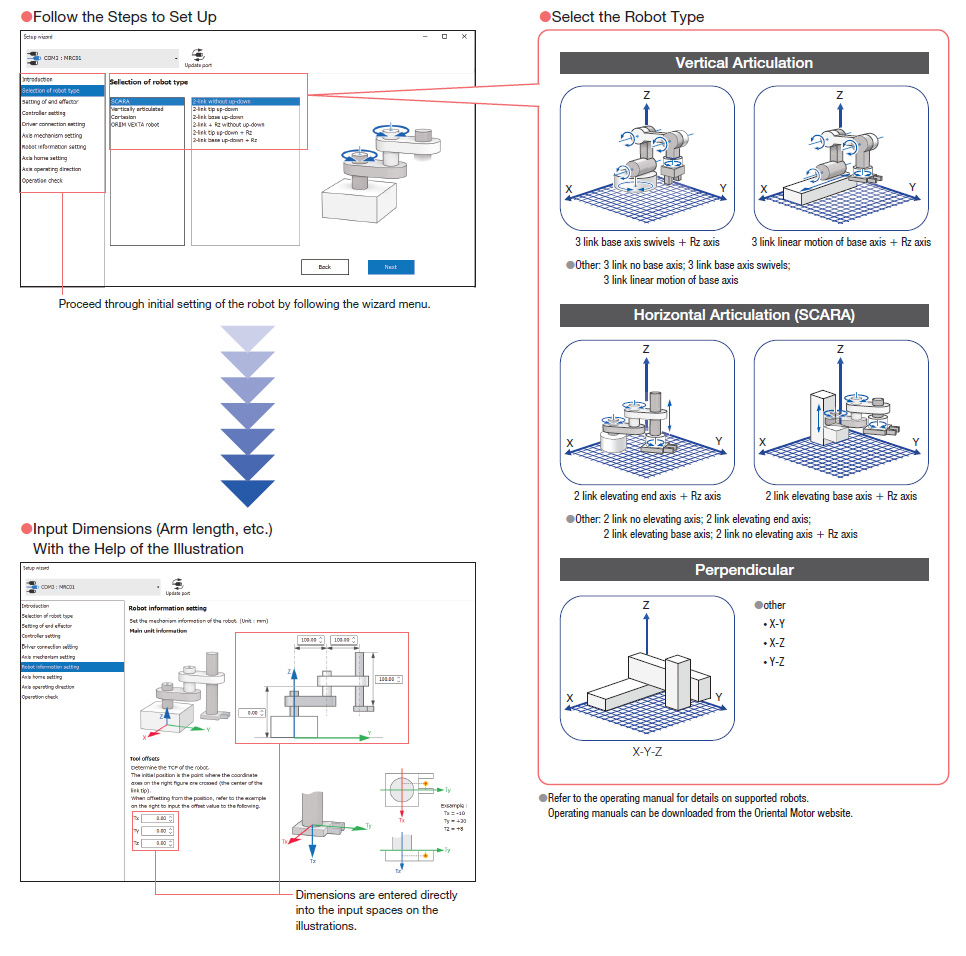
STEP 2 - Say Goodbye to Ladder Logic! Select Items to Program Operation.
Program creation uses a simple command selection format. Programs can be created intuitively, without requiring specialized knowledge such as ladder diagrams. The system supports P to P operation, linear interpolation operation, circular interpolation operation, arch motion and others.
Operating data is executed directly from a host controller via EtherNet/IP.

STEP 3 - Check Operation with an Online 3D Simulator.
The robot’s operation program can be checked using a 3D simulator. The program can be checked easily before the actual robot is activated.
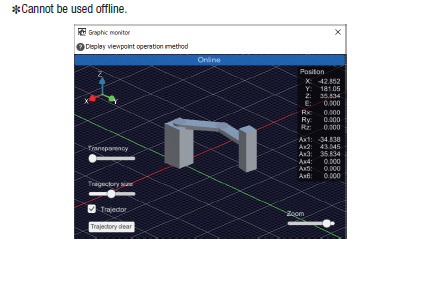